The necessary degree of chain tension, although the years of exploitation of the tillers showed a rare need for such operations, I seek in the following order. Loosen retaining bolts M16. Turning the nut on the M14 bolts welded to the housing shaft of the chassis, pull the chassis circuit. Then the nuts on bolt M14 curly bracket adjust chain tension gearbox. After this the retaining bolts are tightened.
The bridge is a combination of body and chassis of the shaft. The shaft housing is welded from a cylindrical holder, two brackets with slotted holes 70×16 mm and two M14 bolts.
Running the shaft rotates in two bearings 180205Е, from axial displacement to hold the two locking rings. At the ends of the shaft are the hubs of the wheels, the left one with the sprocket driven by the gearbox. Hub nuts with attached lock washers.
The controls consist of two units: lower and upper. The bottom includes a lever starting the engine, held in the transport position, the rubber retainer on the casing of the engine cooling, as well as leverage the re-vers-reducer and gearbox, which are located on the panel, screwed to the body of the gearbox. The last two of the switch lever by the driver’s legs “humpbacked”.
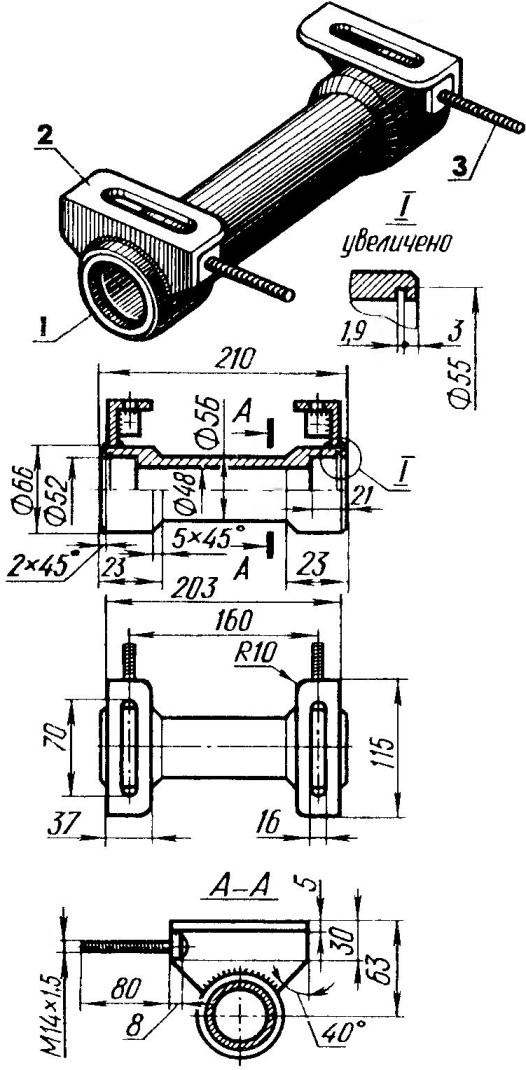
Body chassis shaft:
1 — ferrule; 2 — bracket; 3 — bolt М14х1.5 chain tension gearbox.
Frame control tillers:
1 —tip thread М16х1,5 mounting frame (2); 2 — rod (pipe 21×2, 2); 3 — hinge wing mounting (2 PCs); 4 — mounting bracket ignition coil; 5 — eyelet electronic switch (2); 6 — bracket fastenings of a fuel tank; 7 — arc (tube 14×2); 8—grip throttle; 9 — the bar top with the mounting holes of the fuel tank; 10—spacer (tube 14×2); 11—clutch lever; 12 — backup (pipe 18×2); 13 — tip threaded 14×1,5 mounting frame; 14 — the crossbar of the lower (pipe 18×2).
Mount the fuel tank:
1 — tank; 2 — piping welded flange of the tank (rubber); 3 — earring push-on; 4 — screw M6 (2 pieces); 5 — bracket tank frame control; 6 —frame of the cultivator.
Wing walk-behind tractor (shown left and right — mirrored):
1 — the support for feet of the driver (rod Ø8); 2 — wing (steel sheet 1,5 s); 3 — slip Mat (corrugated rubber); 4 — a bolt M5 (4x); 5 — bracket of the front; 6 — back bracket; 7 — liner front-side (wire Ø3); 8 — liner rear (rod Ø8).
Hinge joint (top view, the plug is conventionally rotated):
] —nut M24; 2 — spacer; 3 — the case of the hinge Assembly; 4 — bearing 180205Е (2); 5 — plug; 6 — washer; 7 — axle; 8 — frame walk-behind tractor.
Upper unit is a control frame, welded from pipes of different diameter. Rod frame is equipped with handles (including handle “gas”) and the clutch lever. For them, the driver of “humpbacked” holds hands. In addition, the frame has different mounting device, which is attached to it fuel tank, ignition coil, electronic switch and rear ends of the wings. And again, on the right side of the drawbar of the cargo truck in a small corrugated pad is the brake pedal (but more on that later).
The cultivator is applied, after small alterations, the exhaust from the fire pump MP-800. It welded the exhaust pipe of the engine, with mounting flange. On top of the muffler are welded two eyelets for attachment to the axles of the motor frame bolt M8.
Wings “humpbacked” have an unusual shape. Covering them is made of steel sheet 1.5 mm thick. the Edges are reinforced rolled them with wire of different diameters. Contact of Shoe soles of the driver with wings covered with rubber mats. To keep the driver’s feet from slipping down, there are special stops. For greater rigidity to the hull inside G welded brackets. Fasten the wings to the frame control (front) and frame tillers (rear) each with two bolts M10. In addition, they have rubber mud flaps.
After heavy use in different conditions revealed certain structural weaknesses of the tillers. Had, for example, to replace the wings on more rigid at the same time finding venues for your feet more comfortable place. Managing tillers easier, as the hands began to help the driver’s foot (new wings shown in the drawings).
And another thing: the walk-behind truck performance on low damp soil. Although he, in fact, not intended for off-road.
However, Gorbunok has served me faithfully for many years. Then, as some of my other designs, moved to a new host. They say the walk-behind still works.
The truck is metal, is welded. Consists of a beam cut from a tube section 43×43 mm, and the frame is assembled from pipe sections section 43×43, 43×26 mm and diameter 49 mm, reinforced with triangular scarves made of sheet steel with a thickness of 5 mm. To the front drawbar is welded a tubular body rotating unit, which the cart connects to the tillers; right — courtesy of thick corrugated steel, which is installed under the brake pedal and brake master cylinder.
Frame with three sides surrounded by a teak pipe with a diameter of 21 mm in eight columns of tubes 18 mm. Handrails pass over the wheels of the truck that allows the transport of oversized cargo. The body is sheathed on the inside (a common tack welding) sheet steel 1.5 mm thick (side and bottom). In the upper edge of the side roll liner — steel wire with a diameter of 3 mm. the Bottom at its rear end reinforced with five longitudinal punch — “the ridge”, which gives it additional rigidity and eliminate the additional force elements.