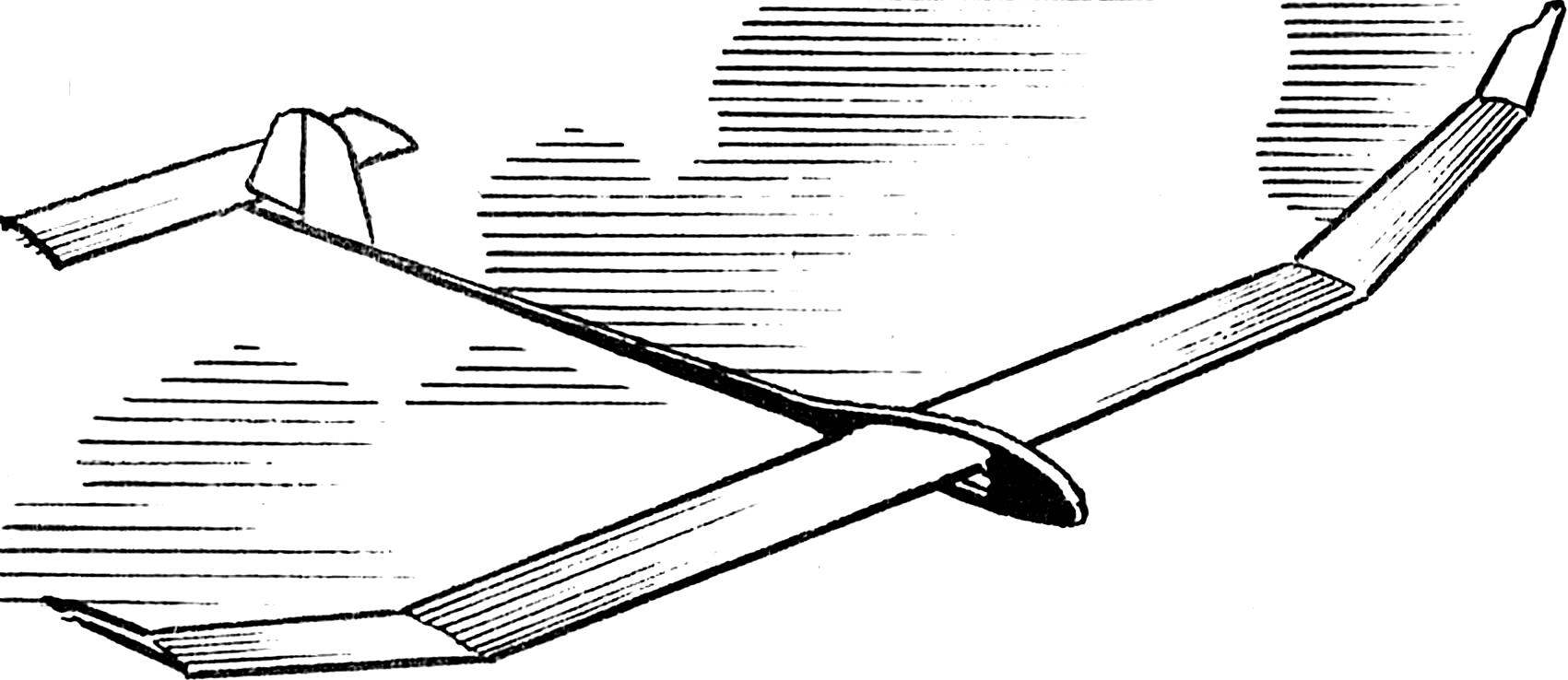
The wing of the model, which brought its creators win at the Championships of the USSR 1989, 1990, success in competitions at the USSR Cup 1990, is a box-like structure. It is made with wide application of composite materials. The caisson of the center section formed of two layers of carbon fabric with a thickness of 0.08 mm with epoxy resin hot curing. The fiber direction of ± 45°. Forming is at a temperature of +180°C, designed for this purpose the electric furnace.
Caisson console molded from a single layer of carbon fabric with a thickness of 0.08 mm (fiber direction along the wing) and is reinforced with carbon filaments in the direction of ±45°.
The spar is constructed from two carbon-shelves of the same size and the balsa walls with horizontal layers. On the edge of the caisson wall reinforced the balsa with two layers up, with fiber direction 0° and 90°. Section shelves of the spars at the root, at the ends of the center section and the console, respectively, 10,5X0,9 mm, 2,5X0,5 mm and 1X0,5 mm.
Of the caisson located inside the balsa leading edge is 2 mm thick balsa noses with a thickness of 1.4 mm.