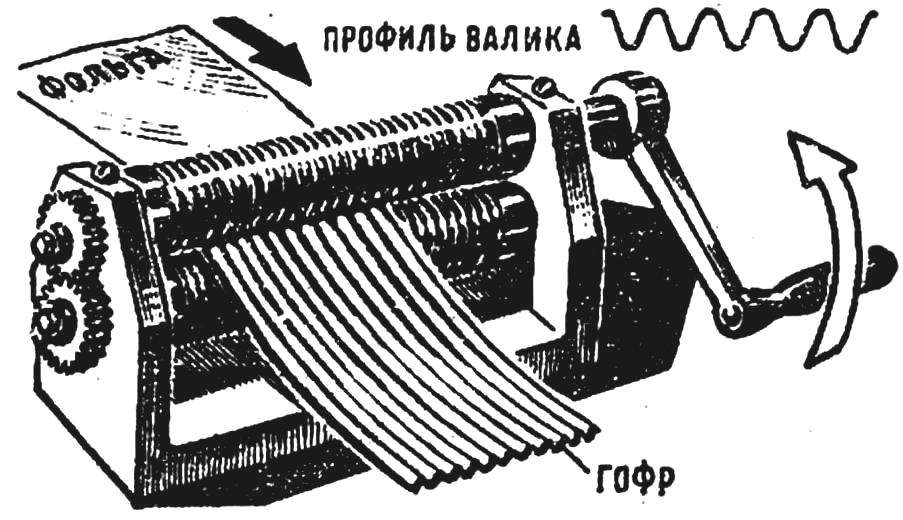
Manufacturer of rolls and boring them require special care. The rolls are handled on a lathe with a chisel triangular shape, the cutting part which on the end is somewhat rounded. Grooves on the surface of the rolls need to carve very precisely: the step of cutting the top and bottom must match. It depends on the scale of the model. So, for models of aircraft TB-1, TB-3, R-6 and others, made on a scale of 1 : 40, pitch is 1.25 mm with a depth of 1 mm.
The screws in the uprights giving the possibility to slightly adjust the gap between the rolls. When rolling it is necessary to select the optimal clearance to the workpiece is not cut and the profile was quite clear. Therefore, before getting to the “rental,” you should make a few samples.
For convenience, the “base camp” better hamstring.
The rolling process is very simple. The strip of metal is introduced between the rollers, and the rotation of the handle is made by rolling. For optimally selected gap is well-corrugated preform, which is clipped in place.
For the manufacture of cladding the metal foil (but not steel) with a thickness of 0.10— 0.20 mm. the Most suitable material is aluminum foil used in printing machines “Era”. But you can use brass and, finally, ordinary drawing paper, pre-coated with nitrocellulose lacquer on both sides and dried.