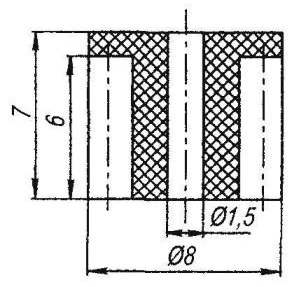
Gradually, as you gain skills, the guys from simple (e.g., a missile) models transferred to the production of more complex motor designs. When creating such models is often to enhance their sports performance in the kinematic chain of the drive propulsion used gear. For example, in performance with increasing rubber motor reducer with gear ratio i = 0,5 allowed twice to increase the speed and the path the model with one complete factory motor (this design is described in detail in the article “Rezinomotornaya “Formula” in the journal “modelist-Konstruktor” No. 2, 1999). And the use of step-down gears (i > 1) ensure, if necessary, reducing the number of revolutions of the engine with increasing torque on the shaft. An example is a model airplane driven by a low-power high-speed (to 20,000 rpm) of the motor.
Unfortunately, in the works of young modelers, this technique finds a worthy place due to technical difficulties of its implementation. Generally, the maximum effect of the gears is achieved with optimal values of gear ratio and parameters of gears and wheels (the module “m” and the numbers of teeth z1 and z2). And where to get such gear?
Meanwhile, the gears of thermoplastics by hot pressing is a good way out of the impasse. Of course, for the responsible competition it is better to use a gear made of metal. But for novice modelers, given the low power of the engines and a small lifetime model with plastic parts can be used with equal success.
In mechanized models tend to apply a fine-grained transmission with a large number of teeth, which reduces friction losses and improve smoothness. For metal gears the module 0.5 mm, for plastic (with less strength) the module is slightly higher.
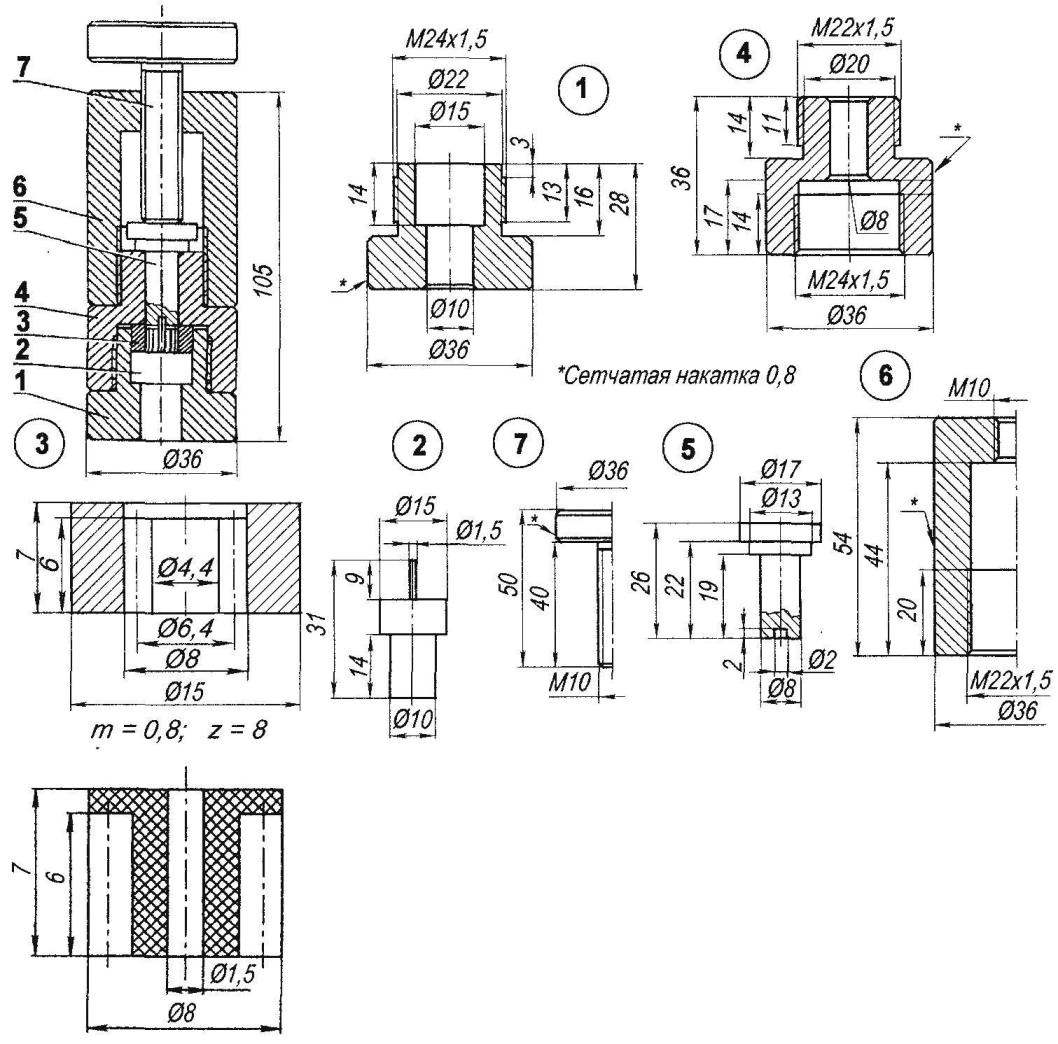
The mold for the manufacture of fine-grained plastic gears:
1—base; 2 — insert; 3 — matrix (bronze, brass); 4—body; 5—plunger; 6—beaker; 7—screw; material of parts 1,4,6,7—steel 45, 40X, range 36; 2,5—round 18
So, to the readers of the journal “modelist-Konstruktor” proposed design of the mold and fabrication of fine-grained (in this case, m = 0.8 mm, z = 8) gears made of polyethylene.
For the manufacture of parts of the mold will require parting off bars of steel 45, 40X diameter of 36 mm (for base, casing, glass and screws) and a diameter of 18 mm (for liner and punch). For matrices it is desirable to use bronze or brass.
All items (except matrix) are machined on a lathe. Such, generally, is in any school workshop. The processing should pay attention to the surface finish and dimensional accuracy providing interface housing with a punch and base with liner and matrix. The only part that probably will not be able to perform their own matrix. To do this, first you need to make a copper master tool: the pivot on which a cut gear teeth with the same parameters that generated the items. Processing the master of the punch must be made on a special gear machine method of running or horizontal milling using a dividing head modular cutter (by copying). Then, in the blank matrix on electrical discharge machine tool with ready-made master of the punch profile is formed the future of gears.
Technology of manufacturing of plastic gears by using the proposed devices is very simple and available even to the students of the 5th class. Collect molds, pre-lubricated with machine oil those surfaces that come into contact with the plastic. First, in the base of the insert liner, and on top of it install the matrix. Then, on the basis of from top to wrap the case up to the stop into the matrix. The hole in the hull filled with raw materials. The raw material can be any thermoplastic (polyethylene, polystyrene, etc.), but preferable to nylon as a more durable and wear-resistant material.
The raw material is best used in the form of pellets. If this is not possible, chopped into small pieces (2×2 mm; 2×3 mm) old toys, bottles, etc., Optimal temperature, providing a viscous-flow state of the plastic material, defined by reference or experimentally. The required amount of raw materials installed by experienced, putting on one of the scales finished part, and the other raw materials, the weight of which should be slightly greater than the mass of the part.
Installing in the housing a punch on the glass and a screw through the plastic plug is compressed to the matrix. Assembled mould to be heated (e.g., in a muffle furnace). The heating time is set empirically. Wearing gloves, pull out the mold, pressed by a screw in the plunger until it stops and sharply cooled in water. After disassembling the mold, the removable part taken from the inevitable dross and get some much needed gear quite satisfactory quality.
V. ARKHIPOV, Severodvinsk